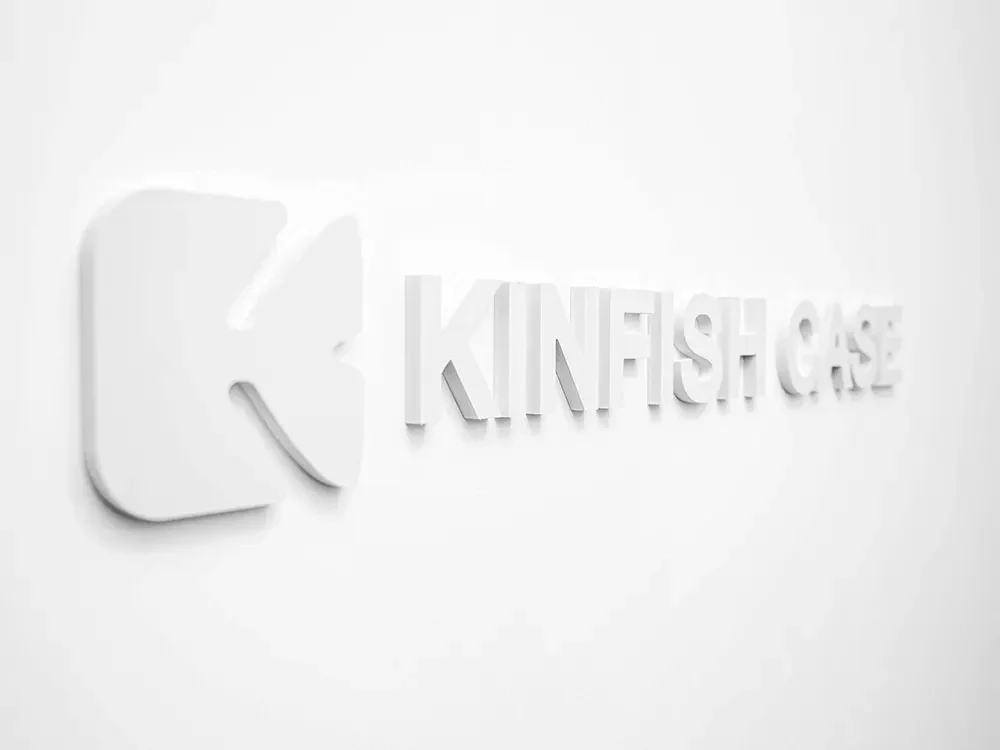
KinFish 케이스 소개
그 이후로 맞춤형 솔루션 제작 2012
“상자 밖에서 생각하십시오.” – 정신은 우리의 DNA를 정확하게 캡슐화합니다. 우리의 사명은 분명합니다: 각 고객만큼 고유 한 맞춤형 케이스 솔루션을 작성하려면, 의료에서 실외 및 소비자 전자 장치에 이르기까지 다양한 시장에 걸쳐. 그것이 우리의 사람입니다 – Dongguan Kinfish Technology Co., Ltd. (KinFish 케이스), 창의적인 운반 케이스 솔루션 & 제조 회사.
Dongguan에 위치하고 있습니다, 중국 5,000 시설의 평방 미터, 우리의 최우선 과제는 항상 품질입니다, 그렇기 때문에 ISO에서 프로세스를 관리합니다 9001 검증 및 제안을 준수합니다 65, 로스, 우리의 자료에 대한 규정에 도달하십시오. 게다가, 우리의 월별 사용자 정의 사례 수율에 도달했습니다 200,000 조각.
그러나 여기에 진정으로 우리를 차별화시키는 것이 있습니다 – 우리는 장거리 운반을 위해 있습니다. 건물 지속, 고객과의 신뢰할 수있는 관계는 우리의 핵심 신념입니다. 그래서, 매끄러운 후에, 엄격한, 또는 맞춤형 EVA 케이스 사이, Kinfish Case는 당신의 파트너입니다. 이 짜릿한 여행을 함께 시작합시다!
사명
의사 소통을하십시오 & 사용자 정의가 더 쉬워집니다.
비전
보호 & 우수성에 대한 열정으로 브랜드를 향상시킵니다.
값
제작 및 디자인을 좋아하는 케이스 건축업자.
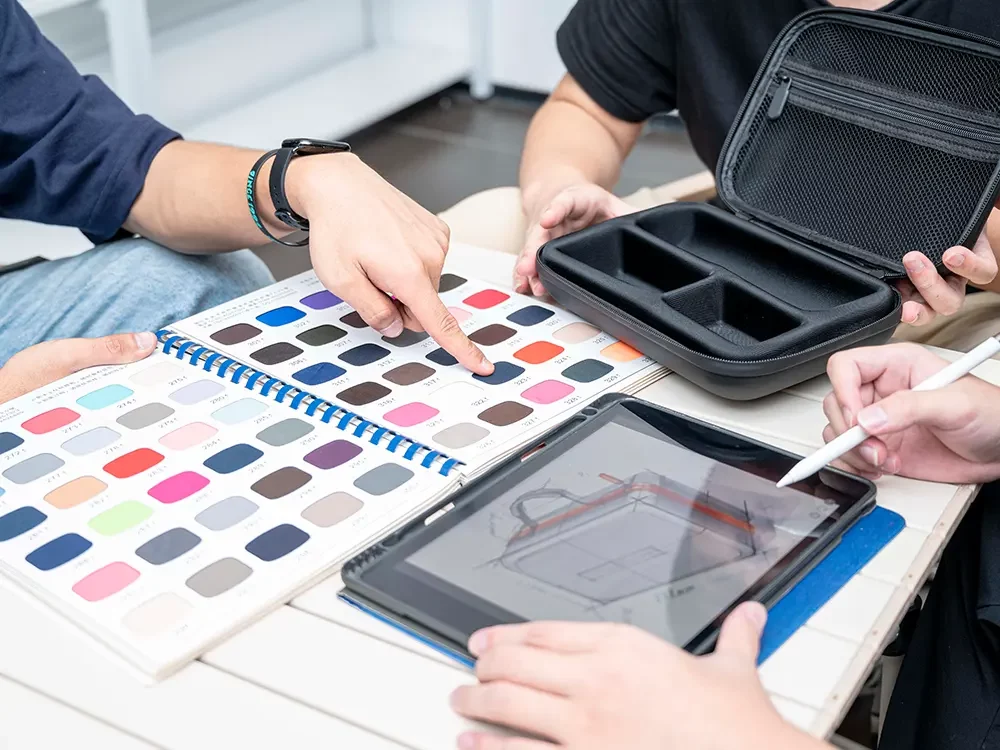
관습은 우리가하는 전부입니다 - 우리의 철학
설계, 그리고 계속 혁신은 우리의 열정입니다
Kinfish Case에 더 가까이 다가 가십시오, Design은 단지 직업이 아닙니다, 우리의 진정한 열정입니다! 우리는 특별한 EVA 사건이 놀라운 미학뿐만 아니라 독특한 “영혼” 그것은 실용적인 가치를 가져옵니다, 우리처럼 인간처럼.
당신이 우리와 팀을 이루면, 효율적인 의사 소통 및 효과적인 문제 해결의 석사 인 경험이 풍부하고 숙련 된 전문가의 뛰어난 승무원을 만나게됩니다.. 이제 여기에 정말 흥미로운 부분이 있습니다: 우리는 동아시아에 기반을두고 있지만, 우리는 서양 일정으로 운영됩니다.
네, 당신은 그것을 바로 들었습니다! 서양 회사와 같은 수준의 전문성과 편의를 누릴 수 있습니다.. 우리는 문화 사이의 다리입니다, 두 세계의 최고를 제공합니다.
그러니 안심하고 창의성으로 가득 찬 짜릿한 모험을 준비하십시오, 혁신, 그리고 많은 재미!
지속 가능성에 대한 우리의 헌신
우리는 에코 전사입니다
Kinfish Case에서, 우리는 탁월한 EVA 사례를 제작하는 것이 아니라 지구를 구하는 임무를 수행하고 있습니다., 한 번에 하나의 사례.
환경 책임에 관해서는 슬리브를 진지하게 멋진 트릭을 가지고 있습니다.. 우리 공장에는 물 소비를 최소화하기 위해 마법과 성가신 산업 폐기물 가스에 마법을 제공하는 첨단 정수기가 장착되어 있습니다.. 하지만 기다려, 더 있습니다! 우리는 세 번째 생명을 얻을 수있는 재료를 수집하고 용도 변경하기 위해 휘젓는 폐기물 전사 팀을 보유하고 있습니다.. 재활용은 우리의 중간 이름입니다!
우리는 환경 평가를 획득 한 중국의 몇 안되는 EVA 사례 제조업체 중 하나라고 자랑스럽게 생각합니다.. 그것은 단지 벽의 인증서가 아니라 지속 가능성에 대한 확고한 약속의 상징입니다.. 우리는 끊임없이 막대를 높이고 있습니다, 어머니 지구를 보호하고 긍정적 인 영향을 미치는 새로운 방법을 찾기.
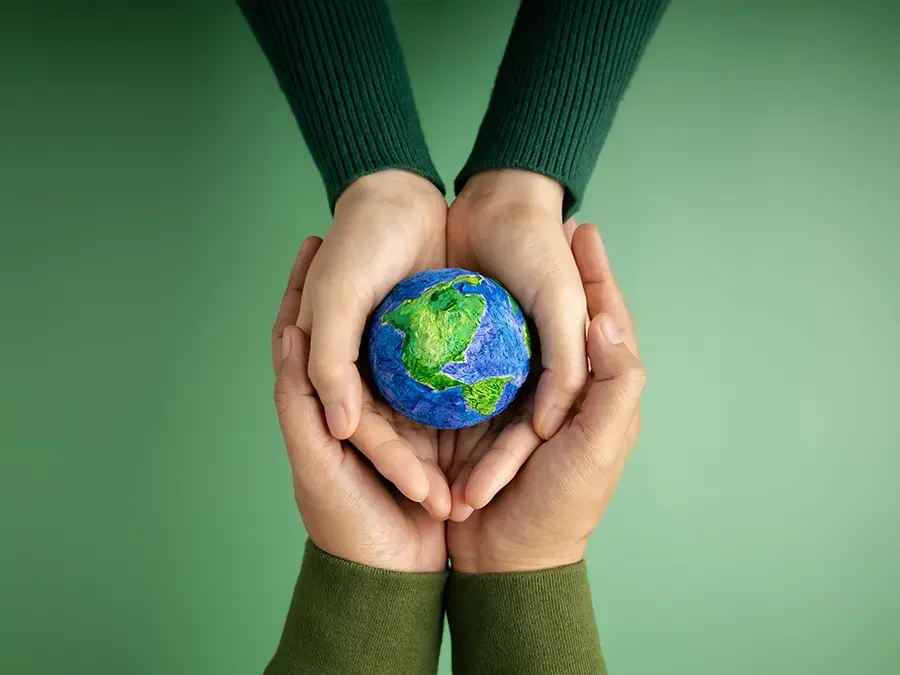
우리의 프로세스를 빠르게 이해하십시오
우리의 맞춤형 Eva Case 공장에서, 우리는 당신의 아이템을 만들기위한 엄격하고 정교한 9 단계 생산 절차를 준수합니다.. 신중한 재료 선택에서 포장의 철저한 검사에 이르기까지, 각 단계는 특정 근로자에 의해 잘 처리됩니다.. 우리가 생산하는 모든 제품에서 우수성에 대한 우리의 헌신.
각 프로세스의 작동 방식을 자세히 살펴보십시오.
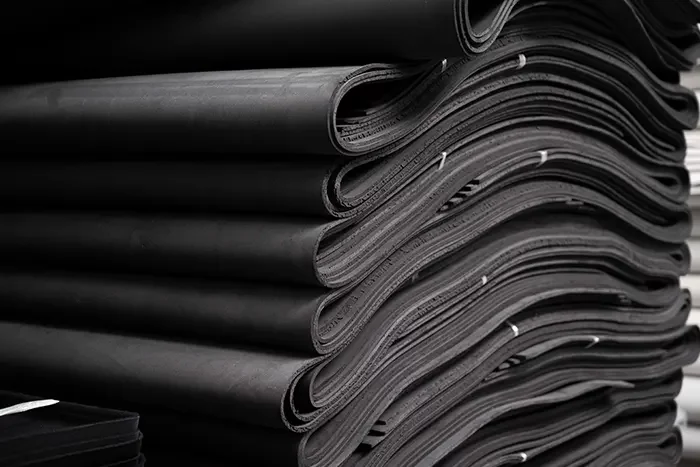
원료
제조 전, 우리는 신뢰할 수있는 공장에서 자격을 갖춘 자료를 공급할 것입니다. 이 원료에는 EVA 폼 시트가 포함될 수 있습니다, 직물, 지퍼, 및 기타 하드웨어 항목.
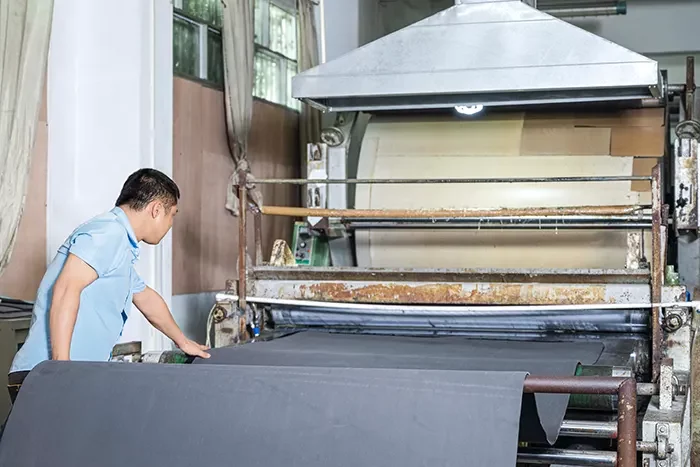
라미네이팅
이 단계에서, 우리의 노동자들은 친환경 접착제를 사용하여 외부 재료와 내부 재료로 Eva 시트를 함께 라미네이트합니다..
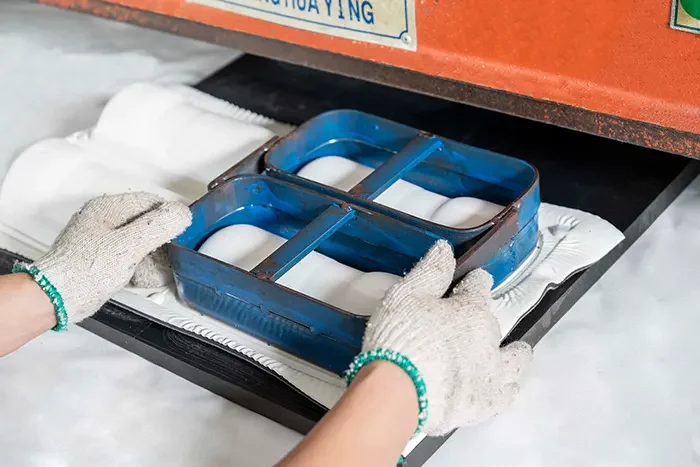
절단
그런 다음 적층 재료를 절단기를 사용하여 필요한 크기와 모양으로 절단합니다.. 정확하고 정확한 절단은 조각을 조립 프로세스를보다 쉽게 만듭니다..
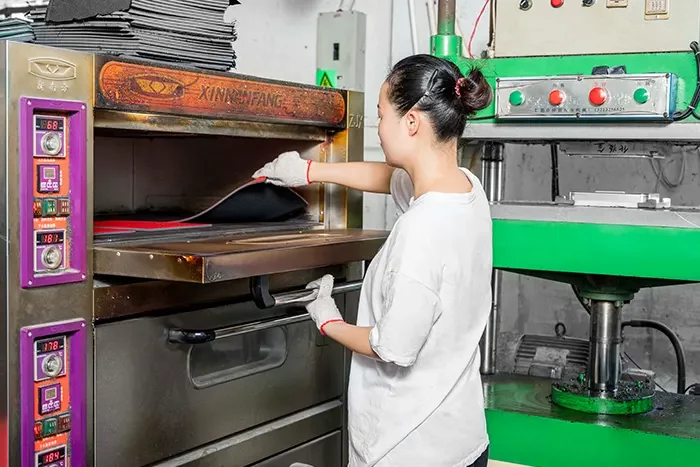
예열
컷 조각은 유연하고 쉽게 곰팡이가되도록 예열됩니다..
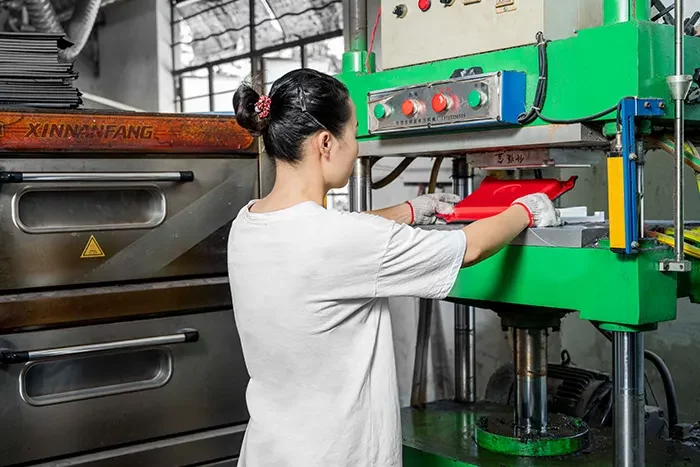
열적 성형
그 다음에, 곰팡이가 요구되는 모양과 크기로 신중하게 설계되었습니다., 자동차 성형 기계는 정확한 모양을 만듭니다.
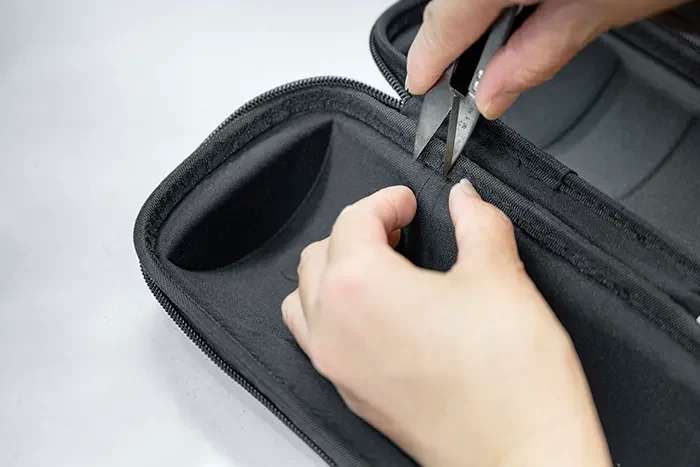
트리밍
성형 후, 초과 재료는 다이 컷 기계를 사용하여 손질됩니다. 그런 식으로, 에바 쉘은 깨끗하고 깔끔해 보입니다.
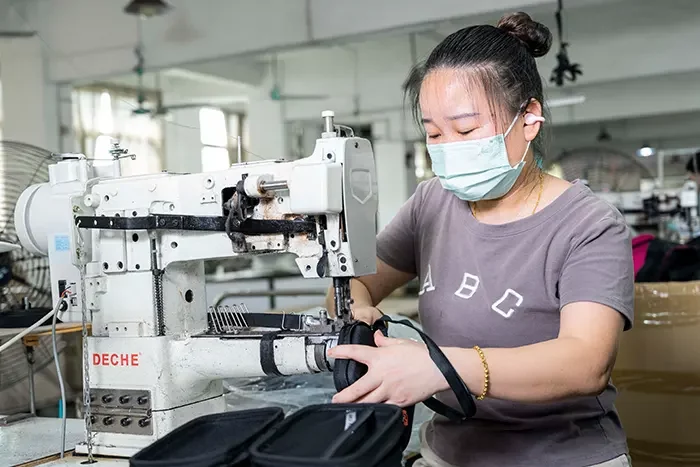
스티칭
그 다음에, 우리 장인들은 재봉틀을 사용하여 다른 조각들을 조심스럽게 꿰매게됩니다.. 이 단계는 케이스가 강력하고 내구성이 있음을 보장합니다..
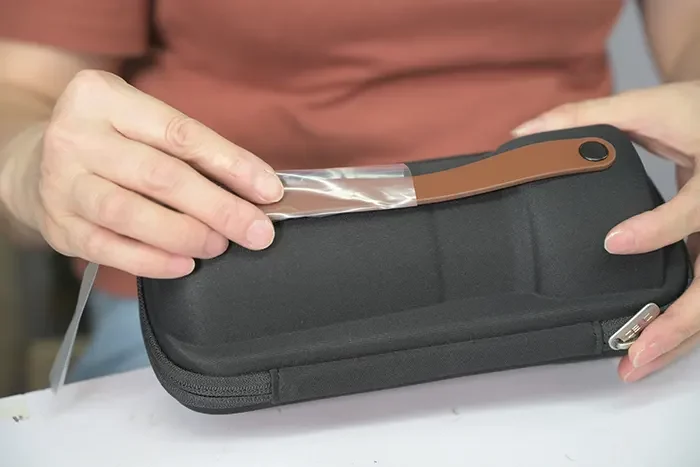
점검
우리 손에서 나오는 모든 제품은 100% 점검. 이 단계에서는 모든 결함이 식별되고 수정됩니다.
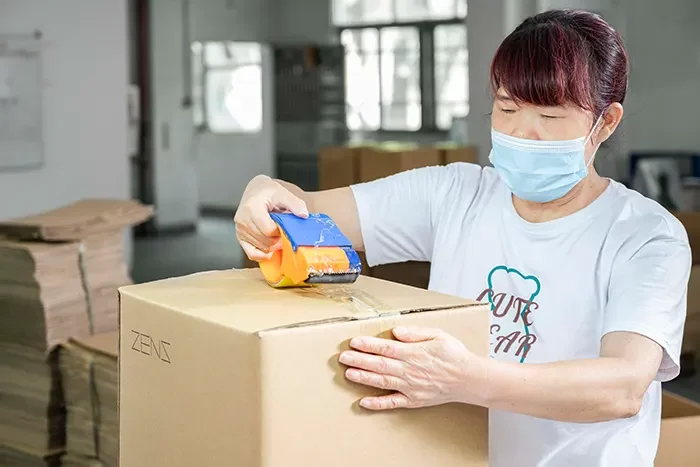
포장
검사가 완료되면, 신중하게 포장 된 EVA 케이스를 행복하게 기다릴 수 있습니다..
우리는 여행합니다, 전시하다, 그리고 파트너 고객과 함께
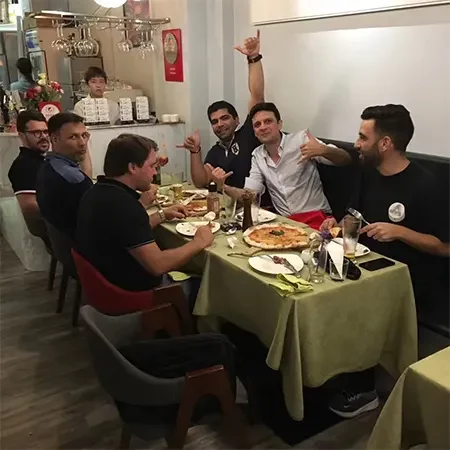
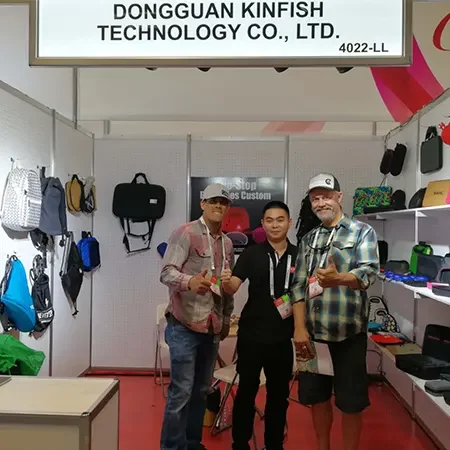
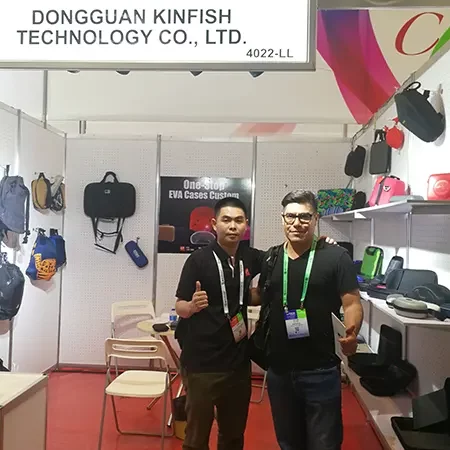
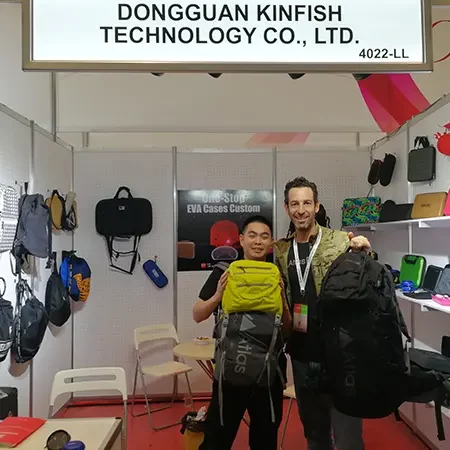
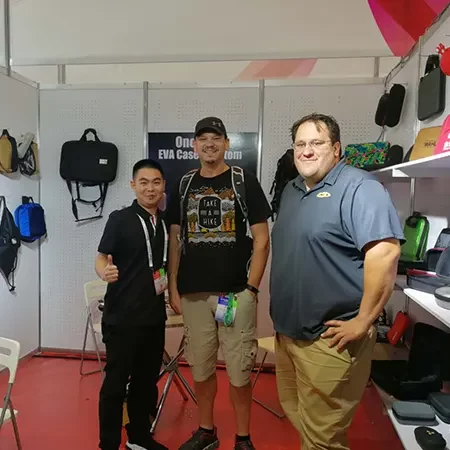
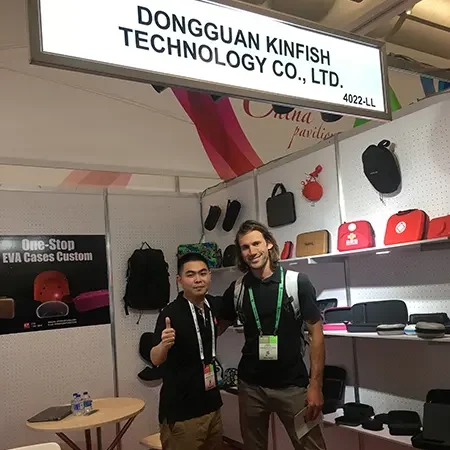
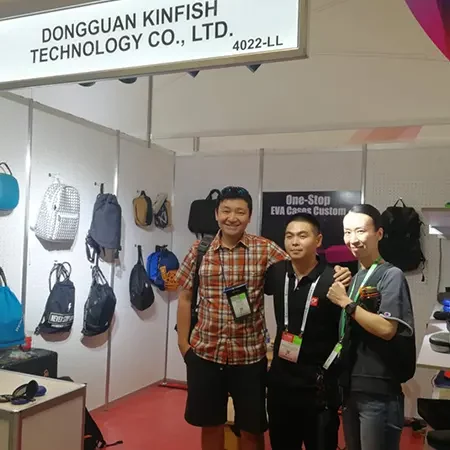