Eva cases have gained considerable popularity in various industries due to their exceptional qualities and versatile usage. In this article, we will take a closer look at the step-by-step process involved in the production of Eva cases, highlighting the meticulous craftsmanship and attention to detail required at each stage.
What is Eva Cases?
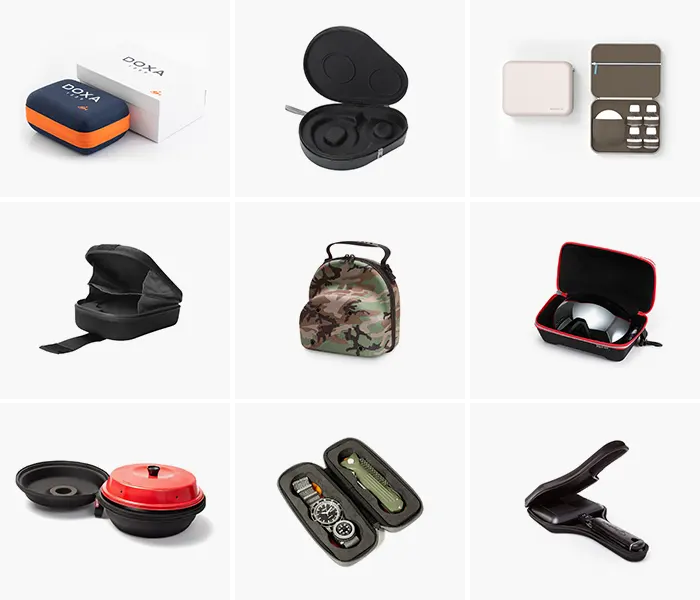
Eva cases are protective storage solutions that are crafted using a material called ethylene-vinyl acetate, or Eva for short. Eva is well-regarded for its durability, flexibility, and unique properties such as impact resistance, water resistance, and shock absorption. These qualities make Eva cases an ideal choice for various industries, including electronics, medical, automotive, and outdoor activities. Eva cases can be customized to fit specific products, ensuring a secure and snug fit, while also offering branding opportunities with a range of colors available. Custom eva cases provide unparalleled protection for valuable items, making them a preferred choice for organizations and individuals alike.
Eva Case Step-by-Step Manufacturing Process
- Material Preparation
- Laminating
- Cutting
- Pre-heating
- Thermoforming/ Molding
- Die-cutting
- Sewing
- nspection
- Packaging
Step 1: Material Preparation
The first step in the production of Eva cases is material preparation. Normally, an EVA shell consists of three layers, exterior material, middle layer EVA, and interior material.
There is a wide range of options available for the exterior material, including choices like multispandex, 600D polyester, 1680D nylon, PU, and more. Additionally, various interior materials such as velvet, multispandex, lycra, and polar fleece can be selected to enhance the functional features of the cases.
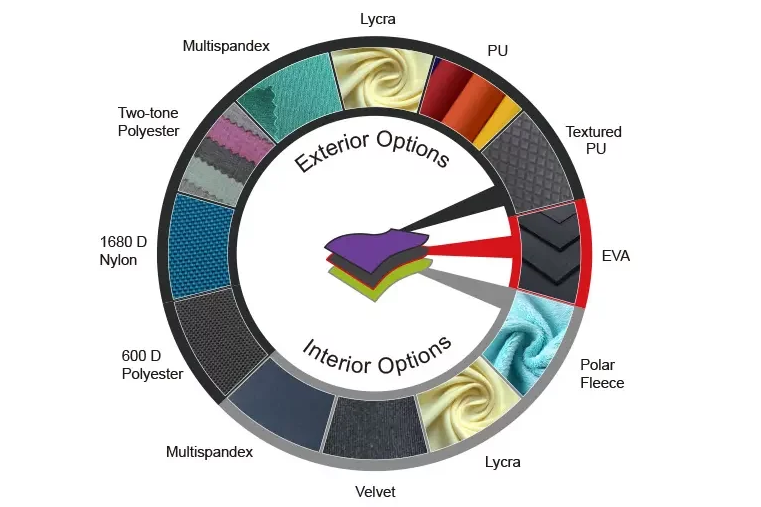
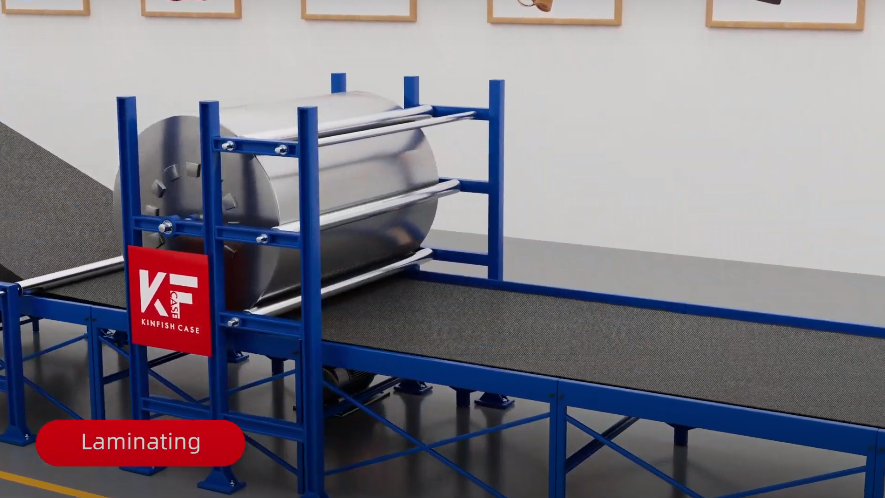
Step 2: Laminating
Once the exterior and interior material are selected, the three layers of the EVA shell are bonded together to reinforce the case structure. This step ensures a secure and reliable construction for the case, as the layers are effectively fused together to create a cohesive unit.
Step 3: Cutting
After the lamination process, the Eva shell sheet is precisely cut into the desired shape using advanced cutting techniques such as die-cutting or CNC (Computer Numeric Control) cutting. This step involves the use of specialized machinery to achieve accuracy and consistency in shape and size. The precise cutting ensures that the Eva hard case fits the intended product snugly, leaving no room for movement or potential damage.
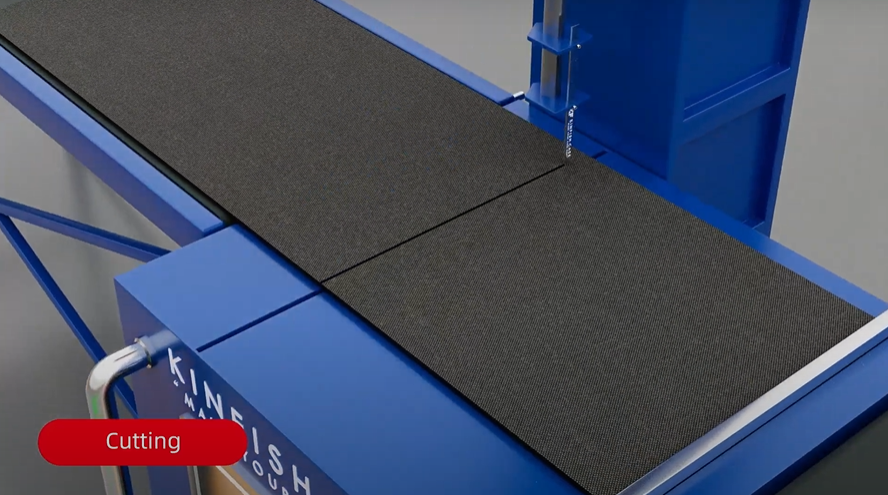
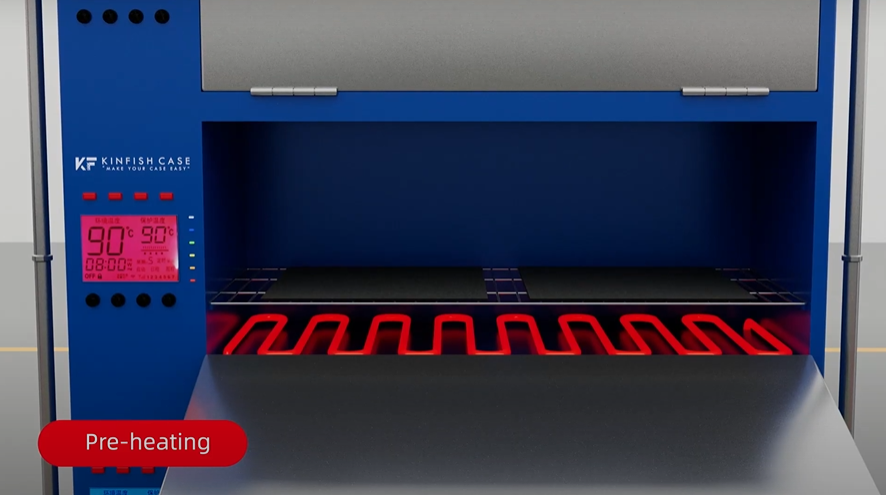
Step 4: Pre-heating
Pre-heating is a critical step in the Eva case manufacturing process. The cut Eva sheets are placed into a pre-heating chamber to achieve the optimal temperature for the thermoforming stage. This pre-heating process allows the sheets to become malleable, facilitating the subsequent molding process.
Step 5: Thermoforming/ Molding
Once the Eva sheets have been pre-heated, they are transferred to a mold. The mold is customized to the specific dimensions and shape required for the Eva hard shell case. The heated Eva foam is then carefully placed into the mold and subjected to a combination of heat and pressure to achieve the desired shape. This thermoforming process ensures that the Eva foam conforms to the mold, creating a precise and custom-fit case.
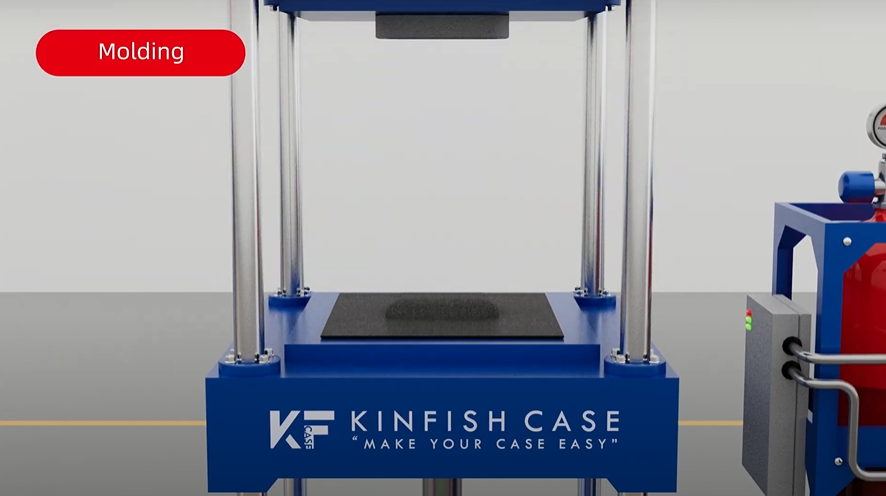
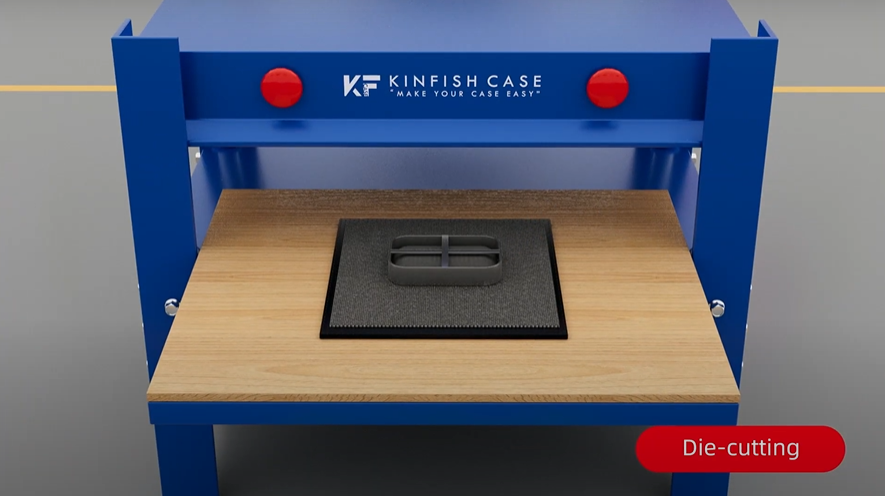
Step 6: Die-cutting
After the thermoforming process, any excess material is removed through die-cutting. Specialized cutting machines equipped with sharp blades precisely trim the Eva foam case to its final shape. Die-cutting provides clean edges and ensures a polished finish.
Step 7: Sewing
Sewing is an essential process that significantly enhances the durability of Eva cases. Skilled craftsmen carefully sew the margins of the case, ensuring a reinforced and secure bond between the layers. This meticulous sewing process plays a crucial role in strengthening the structural integrity of the Eva case, making it highly durable and long-lasting.
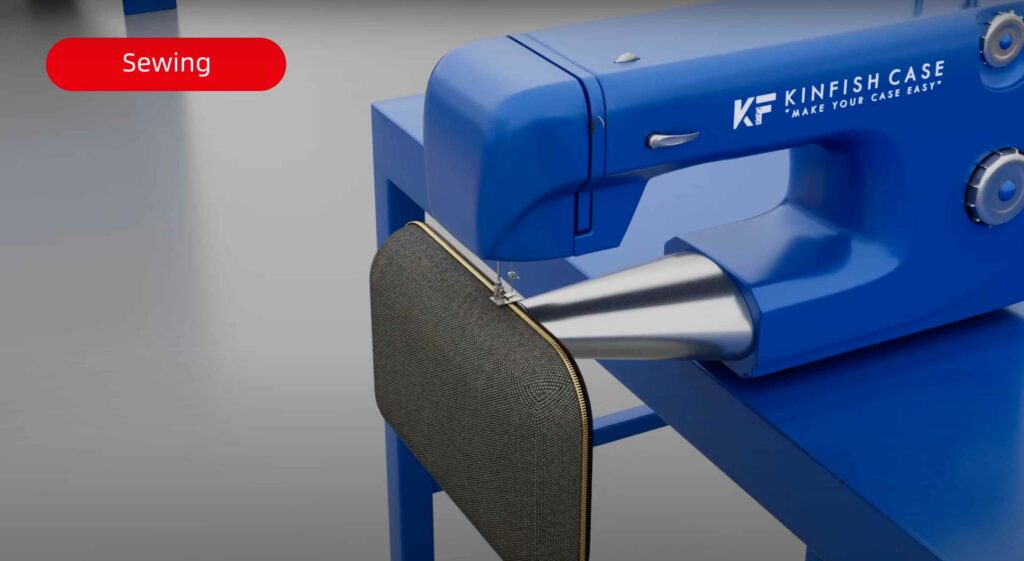
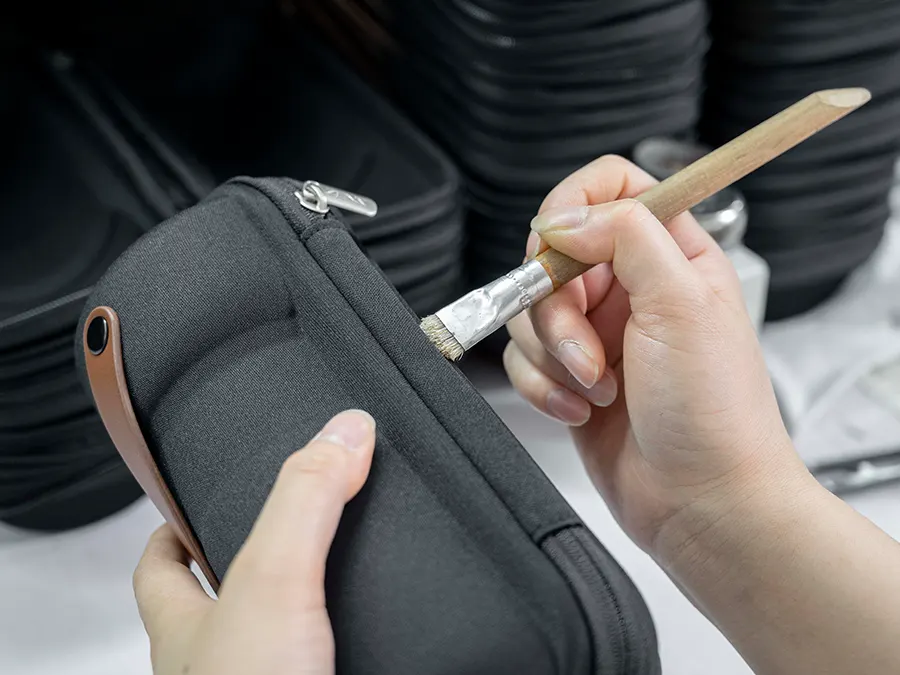
Step 8: Inspection
Quality is of utmost importance in the production of Eva cases. An exhaustive inspection is conducted to evaluate each case’s elements, including zipper quality, stitch density, and overall appearance. Zipper quality ensures smooth and secure closure, while stitch density guarantees the case’s longevity. The appearance inspection ensures that the Eva case meets aesthetic standards, reflecting the brand’s image. Only cases that pass the rigorous inspection are deemed fit for the market.
Step 9: Packaging
Once the Eva cases have undergone thorough inspection and meet the required standards, they are carefully packaged to ensure safe transportation and storage. Custom-designed boxes or wrapping materials are used to protect the cases from scratches or any other potential damage.
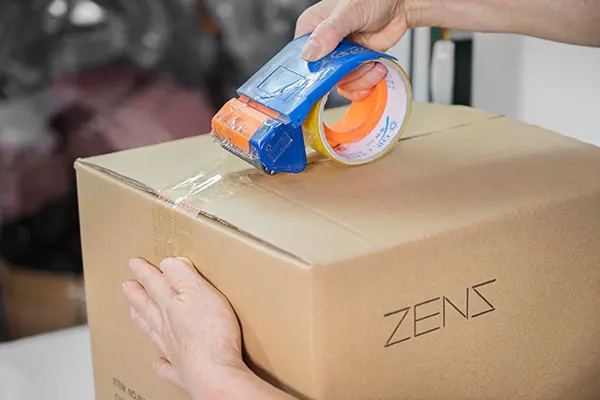
Why Choose Eva Cases?
Eva cases have become highly sought-after and widely acclaimed across numerous industries. Let’s delve into the myriad of benefits that Eva cases offer, making them an indispensable asset for businesses and individuals seeking reliable and protective storage solutions.
- Unparalleled Protection: Eva cases offer unparalleled protection, with their shock-absorbent nature effectively safeguarding valuable items from potential damage caused by impacts or mishandling.
- Durability and Longevity: Constructed from high-quality materials, Eva cases are durable and long-lasting, able to withstand daily use and protect tools, equipment, and devices from wear and tear.
- Customization and Precise Fitment: Eva cases can be customized to precisely fit specific products, ensuring optimal protection and organization. Additional features such as compartments and dividers can be incorporated to enhance functionality.
- Water Resistance: Eva cases are highly water-resistant, providing effective protection against moisture, accidental spills, and exposure to wet environments, making them ideal for industries where liquid damage is a concern.
- Lightweight and Portable: Eva cases are lightweight, making them convenient and easily portable without compromising on protection. They offer a hassle-free storage solution for professionals on the move.
- Branding Opportunities: Eva cases allow for branding with a wide range of color options and the inclusion of logos, graphics, or other elements to showcase brand identity and enhance recognition.
- Versatility Across Industries: Eva cases are versatile and applicable across various industries such as electronics, medical, automotive, and outdoor equipment. They ensure the safety of valuable items regardless of the industry’s specific needs.
Conclusion
The production of Eva cases involves a meticulous and intricate process, emphasizing the highest standards of craftsmanship. From material preparation to packaging, each step plays a vital role in creating durable, versatile, and visually appealing cases. Eva cases’ unique characteristics and customizable nature have made them the preferred choice for various industries, offering unparalleled protection and branding opportunities.